

The Mold Certification procedure should be performed at the mold builder to expedite any required mold modifications and to help avoid delays during mold installation, process start-up and process optimization procedures. Dimensions for the mold mounting bolt holes and the bolt hole pattern in the mold backing plates are verified to help avoid machine scheduling delays during mold installation, initial start-up and process optimization procedures. Cavity and neck insert dimensions, mold cooling channel diameter dimensions, cooling line connector diameter dimensions, mold backing plate mounting hole pattern, mounting bolt hole diameter dimension and mounting bolt hole thread type should be verified with the mold and blow molding machine platen prints. The purpose of Mold Certification step is to verify cavity and mold base dimensions and materials of mold construction.
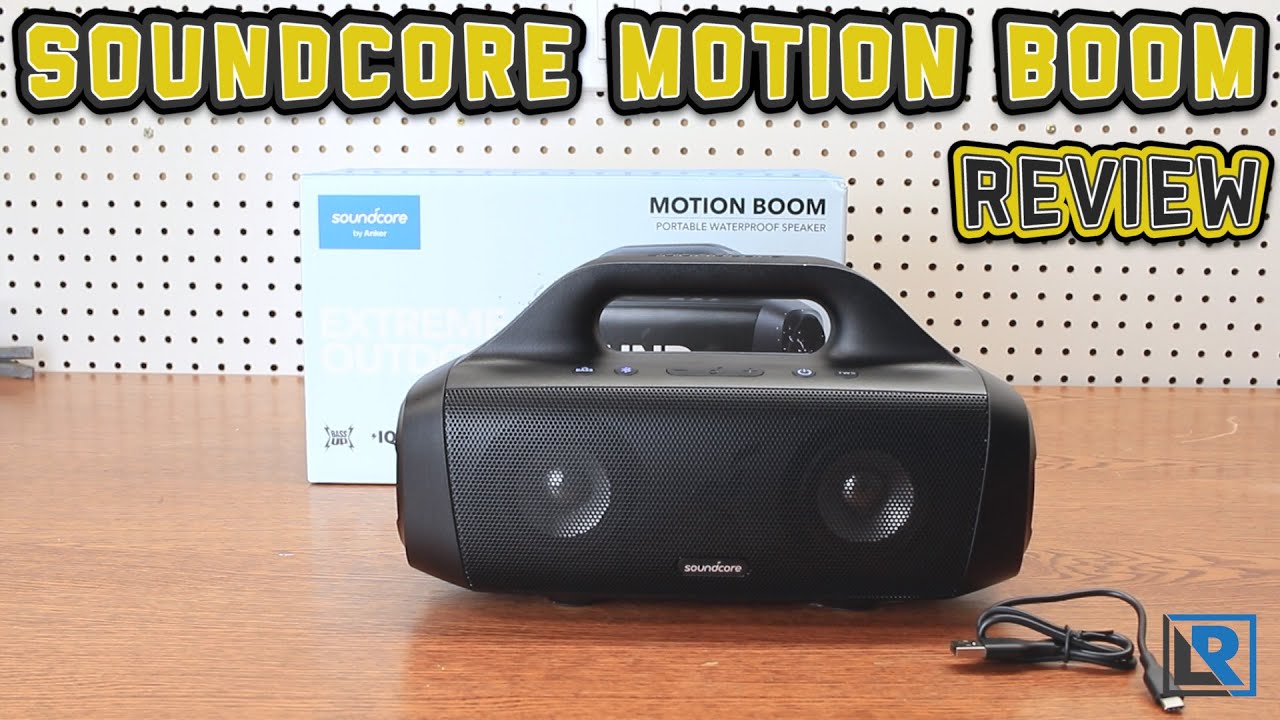
The following steps are required in validating a blow mold with the overall process shown in figure 1:Ĥ.2 Mechanical Mold, Head Tooling and In-Mold Labeling Debug (page 10)Ĥ.4 Qualification (Process Capability Study) (page 48)Ĥ.5 Mold/Neck/Push-up Steel Adjustments (Process Centering) (page 62)ĥ.1 Table of Constants and Formulae for Control Charts (page 65)ĥ.2 Control Chart Interpretation: Three Basic Rules -> C, P, R (page 66)ĥ.4 Capability Analysis Cookbook (page 68)ĥ.5 Standard Normal Distribution Table (page 69)ĥ.7 Example of DOX worksheet for process conditions and variables (page 71)ĥ.8 Safety Precautions For Blow Molding (page 72)ĥ.9 Glossary of Blow Molding Terms (page 73) One of the goals of the Validation Procedure for Blow Molds is to develop a common platform for mold and process evaluation and to maintain efficient communication practices. The document may be used as a reference resource after the methods have been successfully implemented. The Validation Procedure for Blow Molds will also serve as a standard for process optimization so that terms, specific procedures and result data formats are defined. Applying statistical methods to evaluate the molds and the process should help identify key process variables for evaluation. The objective of the Validation Procedure for Blow Molds is to determine molding process conditions that provide production personnel maximized process capability and process adjustment range while maintaining a capable, controlled process. In addition, the molds will have a window of process variable settings that will provide parts within specification. Some combination of settings for these process variables will provide an optimum molding process capable of producing molded containers to within container specifications. Melt Temperature Extrusion Rate Mold Temp Blow PressureĬoolant Temperature Coolant Water Rate Coolant Temp Melt Pressure Temperature Flow Rate Cooling Rate Pressure The blow molding process is a complex process that is controlled by four categories of processing variables: Temperature, Flow Rate, Cooling Rate, and Pressure. Parison Extrusion -> Mold Close -> Parison Blow -> Cool -> Mold Open -> Part Ejection
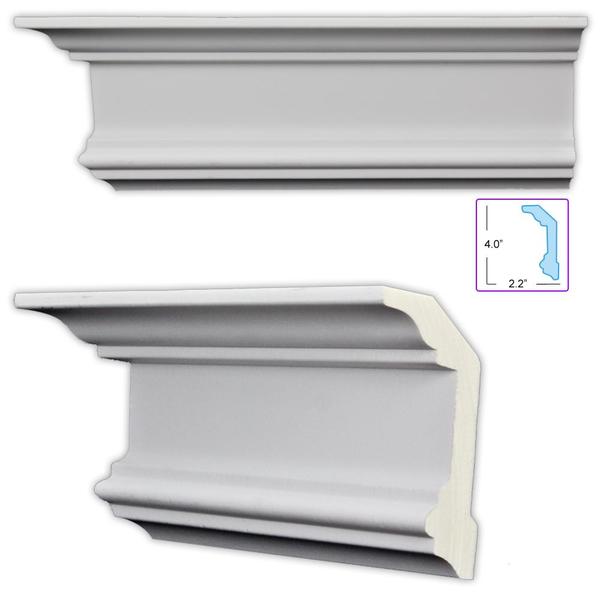
Examples are provided for each step of the mold qualification process to assist in understanding the procedure and qualifying the mold.ġ.2 The extrusion blow molding cycle is broken up into the following segments: Please make use of the glossary at the end of the document to better define terms. It should be recognized that training in design of experiments and statistics, e.g., interpretation of control charts, is needed and that terminology in the blow molding industry varies throughout different regions of the world. This document provides a detailed description of the steps that will deliver the types of results a qualification process is designed for. It is also the purpose of the Validation Procedure for Blow Molds to establish a processing-window for the blow molds. perform the MCA (Multicavity analysis) PCA (Process capability Analysis)activity to validate any moldsġ.1 The purpose of the Validation Procedure for Blow Molds is to identify a capable mold and process that will achieve key part dimensions, attributes and weight. Yes Mold validation is very Important to avoid any Future Quality & production Related problem, But as actual we always Noticed that due to short period of time you can say customer want mold As early as possible, There always many parameter you will face problem so Question is that Is all the molds need to be verified I will say Yes, There is Many scientific way to validate the Injection, Blow molds Simple way to analysis the process parameter which is required to get the desired Quality.
